In today's rapidly advancing technological landscape, 3D printing technology has swept across various industries like a powerful east wind. From intricate and precise mechanical parts to lifelike product models, from dreamlike architectural prototypes to personalized daily necessities, 3D printing technology, with its boundless creativity and sufficient flexibility, has brought imagination to reality, making life more convenient and surprising us at the same time.
Working Principle of 3D Printing Technology
3D printing technology, also known as additive manufacturing technology, constructs three-dimensional objects by stacking materials layer by layer, representing an innovative production method. Its principle is similar to building a brick house and can be simply summarized as "layered manufacturing, layer by layer."
The 3D printing process is not complicated. First, a digital model is created or obtained through computer-aided design software. Then, the model is cut into a series of very thin cross-sectional layers (i.e., slicing), with each layer thickness typically ranging from tens of micrometers to hundreds of micrometers. Next, the 3D printer constructs the final object layer by layer according to these slicing information, using specific techniques and materials.
Advertisement
3D printing technologies include Fused Deposition Modeling (FDM), Stereolithography (SLA), Digital Light Processing (DLP), and Liquid Crystal Display (LCD) 3D printing, Selective Laser Sintering (SLS), Selective Laser Melting (SLM), 3D Inkjet Printing (3DP), and Laminated Object Manufacturing (LOM).Fused Deposition Modeling (FDM) is a technology that heats and melts filamentous thermoplastic materials through a nozzle, depositing them layer by layer on a platform until they solidify into a three-dimensional object. Common thermoplastic materials used as raw materials include Acrylonitrile Butadiene Styrene (ABS), Polylactic Acid (PLA), etc. This technology requires relatively low equipment and is easy to operate, making it suitable for personal and small studio use. Recently popular toys in the market, such as "carrot knives" and "telescopic swords," are made through this method.
Stereolithography (SLA), Digital Light Processing (DLP), and Liquid Crystal Display (LCD) 3D printing use specific wavelengths and shapes of light to irradiate photosensitive resins. The photosensitive resins solidify layer by layer to create objects of the desired shape. This technology has high molding accuracy and smooth surfaces, making it suitable for making fine models and small parts.
Selective Laser Sintering (SLS) uses a laser beam to scan powder materials, causing them to melt and bond together, accumulating layer by layer into a three-dimensional object. This technology uses powder as raw materials (such as nylon, metal powder, ceramic powder, etc.), has high molding accuracy, and is suitable for manufacturing complex structural functional parts.
Selective Laser Melting (SLM) has higher laser energy, similar to Selective Laser Sintering (SLS), and can completely melt metal powders to achieve rapid prototyping of metal parts. This technology commonly uses metal powders (such as titanium alloys, stainless steel, etc.) as raw materials, and can print high-strength, high-precision metal parts, widely used in fields such as aerospace and medical.
Three-Dimensional Inkjet Printing (3DP) uses powder materials (metal or non-metal) and binders as raw materials, utilizing the binding mechanism to print each part layer by layer. The samples formed by this printing technology have the same color as the actual product and are currently a more mature color 3D printing technology.Laminated Object Manufacturing (LOM) uses thin materials such as paper sheets and plastic films, along with hot-melt adhesives, to create objects through laser cutting and thermal bonding, layer by layer. This technology is fast in forming and has low material costs, making it suitable for the production of large structures and casings.
Despite the high fidelity of 3D printed products, they are often brittle and prone to fracture under external forces due to the limitations of the printing materials. When these products are applied in scenarios that demand high mechanical performance, they may seem somewhat "inadequate." So, how can we improve the "fragility" of 3D printed products, so that they not only have an attractive "appearance" but also possess "flexibility" that is not easily broken?
On July 3, 2024, Chinese scientists published a research result on 3D printed elastomers in the journal "Nature." The rubber bands made using this technology can be stretched to nine times their original length, with a maximum tensile strength of 94.6 MPa. This is equivalent to one square millimeter being able to withstand nearly 10 kilograms of force, demonstrating an extremely high level of strength and toughness.
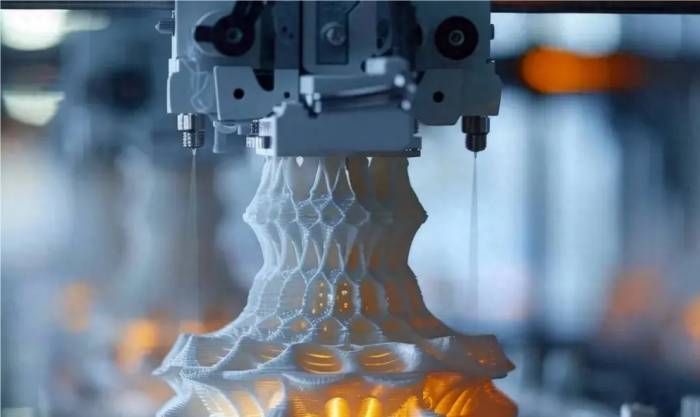
"Reconciliation" between molding speed and finished product toughness
In the process of photo-curing 3D printing (SLA, DLP, LCD), increasing production efficiency requires a faster molding speed, which leads to an increase in cross-linking density during the curing process and a decrease in material toughness. Under conventional methods, as material toughness increases, material viscosity also increases, resulting in reduced fluidity and slower molding speed. The contradiction between 3D printing molding speed and the toughness of the finished product has always troubled the entire industry.Chinese scientists have achieved a "reconciliation" between these two contradictory points. Researchers, through the analysis of photopolymerizable 3D printing raw materials such as photosensitive resins and the disassembly of the printing process, proposed a strategy for phased printing and post-processing. Researchers designed a DLP (Digital Light Processing) precursor of dimethacrylate, which contains dynamic hindered urea bonds and two carboxyl groups in the main chain. During the printing and molding stage, these key components are in a "dormant" state and play a toughening role in the post-molding treatment stage.
During the post-processing stage at 90°C, the hindered urea bonds in the 3D printed products dissociate to form isocyanate groups. On the one hand, these groups form amide bonds with the side chain carboxyl groups, and on the other hand, they react with the water absorbed by the carboxylic acid to form urea bonds. The chemical bond changes occurring within the molecules connect the single network structure in the material into an interlocking network structure similar to "hand in hand," bringing more hydrogen bonds and strengthening the internal structure of the material. It is precisely because of the changes in the internal structure of the material that the 3D printed products have a larger buffering space when deformed under external forces, similar to the energy absorption effect during vehicle collisions, which improves the product's impact resistance and fracture resistance, and has higher toughness.
Experimental results show that the ultra-thin film with a thickness of only 0.8 millimeters, prepared by 3D printing using the DLP precursor, exhibits extremely strong puncture resistance, allowing it to withstand a force of 74.4 Newtons without breaking. Even under high-pressure inflation conditions, the 3D printed pneumatic clamp can still pick up a copper ball with sharp thorns on the surface and a weight of 70 grams without breaking, demonstrating the ultra-high toughness and structural strength of 3D printed products.
Wide application of 3D printed elastomers
In the field of sports equipment, 3D printed elastomers provide athletes with personalized, high-performance equipment. For example, customized insoles and protective equipment utilize the shock absorption and support characteristics of elastomers, which can optimize athletes' performance and enhance the wearing experience. Especially in extreme sports and high-impact sports, 3D printed elastomer materials can significantly reduce the impact on athletes during sports and protect their joints and muscles from injury.In the automotive and aerospace sectors, 3D printed elastomers are utilized for lightweight shock-absorbing components and seals, among other critical parts. These parts, through intricate structural design, are capable of reducing weight while maintaining high performance.
In the electronics industry, smart speakers, smart bracelets, and phone cases can all be printed using elastomeric materials. These products not only possess excellent softness and elasticity but also have high wear resistance and durability, meeting consumers' multifaceted demands for product aesthetics and performance.
In the field of industrial manufacturing, 3D printed elastomer technology is employed to fabricate various industrial molds and conveyor belts, among other components. These components are required to withstand significant mechanical stress and vibrations, and elastomeric materials, with their superior elasticity and fatigue resistance, are the ideal choice. Producing these parts through 3D printing technology not only enhances production efficiency but also reduces manufacturing costs.
The advent of 3D printed elastomer technology has further expanded the range of applications for 3D printed products, bringing a more colorful array of possibilities to our lives.