The high-speed rotation of the cutting tool stabilizes and advances, and the hard metal under the blade seems as compliant and smooth as butter. As the chips and cutting fluid splash, the bright and shiny parts are liberated from the metal blank, and then assembled into machines—each part with precise dimensions interlocking perfectly, with no looseness between them yet running smoothly...
Even friends who are not engaged in the related industry will feel satisfied when they see such a rigorous processing and manufacturing process. The main reason for this rigorous and smooth pleasure is two words—"precision". High precision means that the machine is more efficient and has a longer lifespan. Many important mechanical equipment have very high requirements for precision.
Recently, the China Association for Science and Technology released the major scientific questions, engineering technical difficulties, and industrial technical problems of 2024. Among the top ten engineering technical difficulties, "Rapid assessment of machine tool precision maintenance" is included. So why is the "precision" of the machine tool so important? Why is it so difficult to maintain precision?
For this, we consulted Professor Liu Kuo from the School of Mechanical Engineering at Dalian University of Technology to interpret these issues of public concern.
Advertisement
Machine tool: Why is precision so important?
The sayings "If the upper beam is not straight, the lower beam will be crooked" and "There are no rules, no circle" fully illustrate that with the correct benchmark, the products will not deviate. The machine tool, on the other hand, bears this important task.
A machine tool refers to a machine that processes metal or other material blanks or workpieces to obtain the required shape, size, and surface quality. It can usually be understood as "the machine that makes machines". Although it does not directly produce end products, it provides basic parts or molds for other equipment, thereby indirectly affecting various manufacturing industries.
Typical complex parts manufactured by machine toolsIt is precisely for this reason that the accuracy and maintenance of accuracy of machine tools are of paramount importance. The term "accuracy," in layman's terms, refers to the degree of precision in "processing according to the drawing"—if the processed parts are exactly the same as the drawing requirements, with perfect flatness and verticality, accurate shape, and no deviation in size, then it can be said to have high precision.
To illustrate with a simplified example, for a lathe, if the external round of a 0.5-meter diameter metal cylinder is turned with an error of less than 5 microns, it can be considered precision machining. And 5 microns is approximately equivalent to 1/16 of the diameter of our hair. Other types of machine tools each have their own standards.
A high-precision machine tool is like an experienced craftsman, capable of finely controlling every detail of the processing process, from the positioning of parts to the precise cutting of sizes, and then to the perfect shaping of the shape, every step strives for precision and error-free. This high precision not only reduces rework and material waste caused by excessive processing accuracy but also significantly improves the overall quality and consistency of the product.
What are the causes of reduced accuracy?
Many friends have the experience that a brand-new bicycle is quiet and labor-saving to ride, but after riding thousands of kilometers, the bike may make noise here and sway there, and the resistance when pedaling is also increased. This is also related to "reduced accuracy," and similar things will also happen to machine tools.
Many mechanical processing videos we see can be described as "cutting iron like mud," although it looks easy, in fact, the machine equipment is under great force.
Under such circumstances, the bolt connection interfaces such as the bed-column, bed-guide rail of the machine tool may have problems such as interface micro-wear, nut rotation loosening, and bolt rod creep during the working process, causing the decline of the pre-tightening force of the bolt, leading to slight deformation at the joint surface, resulting in the decline of the machine tool's accuracy.
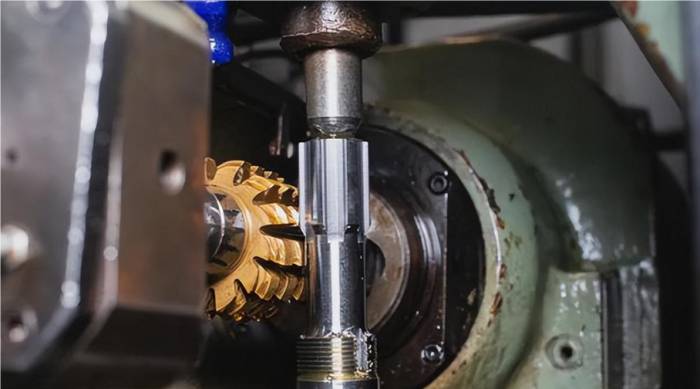
In addition, when the machine tool processes parts, there will be many movable moving parts, such as common lead screws and nuts, sliders and guide rails, etc. With the long-term operation of the machine tool, the contact surface of the moving parts will gradually wear, causing the original precise fitting state to change, resulting in the decline of the machine tool's accuracy.
So, can the machine tool not work or work less to reduce wear and accuracy decline?Not necessarily so.
The bed, column, and other large structural components of the industrial mother machine must undergo processes such as casting, rough machining, and precision machining. Often, a significant amount of residual stress remains within the basic components. If not adequately treated with aging processes, these internal stresses will gradually release during the service life of the industrial mother machine, causing changes to the original installation benchmarks regardless of whether the machine is operating or not, leading to a decline in the machine tool's accuracy.
If there are issues with the precision of the industrial mother machine, it will affect the accuracy of the processed parts and the quality of the final product—the parts may have dimensional deviations, shape distortions, and other issues, causing the product to fail to meet the expected performance requirements.
These inaccurately processed parts, when installed in machinery, can lead to decreased efficiency, increased wear, vibration, and noise, which not only affects the performance and normal use of the machine but also reduces its lifespan and can even bring potential safety hazards.
Especially in precision manufacturing industries such as aerospace, national defense, and automotive, such quality issues may lead to serious safety risks and even catastrophic consequences.
It is precisely for this reason that we need to regularly inspect and maintain the mother machine to ensure accuracy. It is easy to think that if we can improve the industrial mother machine to maintain accuracy over a long period, it would increase efficiency and reduce costs, which is of great significance to the industry.
However, this is not an easy task.
Why is maintaining accuracy so difficult?
Taking the precision gantry machining centers and horizontal machining centers widely used in aerospace, automotive, and other fields as an example, more than half of the domestic machining centers on the market today have obvious shortcomings in maintaining accuracy, often lasting less than a year, which is in stark contrast to the precision maintenance performance of more than 5 years for high-end foreign counterparts.
This gap not only affects the overall quality of China's high-end manufacturing products but also severely restricts the technological progress and development speed in related fields.So, why is it so difficult to maintain precision?
Firstly, although we usually only talk about "industrial mother machine precision," the industrial mother machine is actually a very complex piece of machinery. There are many types of precision, including but not limited to positioning accuracy, straightness, perpendicularity, and spindle rotation accuracy. Each precision index is directly related to the machining quality and efficiency of the machine tool, but the way they contribute to machining performance and the degree of influence are different.
Secondly, the maintainability of precision is closely related to various aspects such as the structural design, component materials, assembly process, and service conditions of the industrial mother machine. Subject to the interaction of various loads such as temperature, vibration, and cutting force during service, the slight deviations in the design and manufacturing process of the industrial mother machine will gradually amplify over the long term, causing irreversible effects on precision. In the end, a small error can lead to a big mistake, affecting the final product.
There are so many complex factors affecting the precision of the working mother machine, so maintaining precision naturally becomes a "step-by-step thrilling" task.
Facing challenges and solving the problem of maintaining precision
After introducing the basic knowledge, we can talk about how to overcome the problem of poor precision maintainability.
In layman's terms, when optimizing equipment, we usually go through these steps: figure out what's wrong, summarize what's prone to failure, understand why it fails, and find ways to prevent it from failing - this cycle continues, and the accumulated knowledge and experience will be directly applied to the next round of design and production processes, trying to discover and prevent various problems and shortcomings from the source, so that the equipment can be better and better.
However, although the above steps sound simple, in practice, for large-scale equipment with complex structures and many precision items like the industrial mother machine, it is very troublesome. In the past, on-site tracking and testing methods were often adopted, but this method has a long cycle and cannot quickly measure the level of precision maintainability and shortcomings, making it difficult for the precision maintainability of domestic industrial mother machines to achieve a leap in a short period.
So, how can we solve this problem? The answer is "accelerate." If we can find a way to shorten the time required for the precision maintainability assessment of the industrial mother machine, we can make improvements in a short time and improve precision.Specifically, theoretically, it is necessary to clarify the laws of precision degradation of industrial mother machines under different configurations, manufacturing processes, and service conditions, to understand the microscopic mechanism of precision degradation of industrial mother machines, and to establish mathematical models to provide a theoretical basis for the study of precision maintenance of industrial mother machines. This will make the research more forward-looking and targeted.
Technically, it is necessary to establish a platform that can accelerate the degradation of precision maintenance of industrial mother machines. For complex mechatronic systems such as industrial mother machines, breakthroughs in the technology of multi-stress accelerated degradation tests for extremely small samples of industrial mother machines are needed. Establishing a test platform for the precision maintenance of industrial mother machines that can simulate actual working conditions and load multiple loads can improve the efficiency of testing.
In layman's terms, it is to use short-term accelerated degradation test data, combined with simulation and digitalization, to achieve overall inference of precision degradation data during the long-term service process of industrial mother machines, which can greatly improve the efficiency of testing.
However, internationally, the products of industrial mother machines in Germany, Japan, Switzerland, and other countries have gone through more than a hundred years of iterative upgrades, and their precision maintenance capabilities have reached a high level, and systematic research on the precision maintenance of industrial mother machines has not yet been carried out.
Domestic research on the laws and mechanisms of precision degradation of industrial mother machines is far from enough, and the research on accelerated degradation test technology for complex mechatronic systems at the machine level is still very weak. The breakthrough of precision maintenance rapid evaluation technology requires a large number of experimental attempts to explore scientific and accurate rapid testing methods.
Taking this route can be said to be facing difficulties head-on, but without the courage to propose and try to solve such difficult problems, it is impossible to achieve the goal of improving the precision maintenance of industrial mother machines in the short term.
At present, Dalian University of Technology, in conjunction with the Smart Manufacturing Longcheng Laboratory, has developed the world's first set of industrial mother machine precision maintenance rapid testing platforms with a load of 20 tons, which can perform multi-stress loading such as temperature, vibration, speed, and static and dynamic forces on industrial mother machines, and is making every effort to tackle the technology of multi-stress accelerated degradation tests for industrial mother machines, and continuously developing a series of precision maintenance rapid testing devices for key functional components of industrial mother machines, striving to build an internationally leading rapid testing base for the precision maintenance of industrial mother machines.
With the support of the new round of the national "04" major projects, it is expected that by 2027, the rapid evaluation technology for the precision maintenance of industrial mother machines will be broken through, a series of national or industry standards for rapid evaluation of precision maintenance will be formulated, and a rapid evaluation base for the precision maintenance of industrial mother machines will be fully built, supporting some special project R&D products to reach an internationally advanced level. It is expected that by 2035, the rapid evaluation technology for precision maintenance will continue to develop, fully supporting domestic industrial mother machines to reach an internationally advanced level, and promoting China's industrial mother machine manufacturing technology level to the forefront of innovative countries.